As the world accelerates toward a future defined by electric mobility, renewable energy storage, and compact high-performance electronics, the demand for more efficient and safer battery technologies is at an all-time high. Among the frontrunners poised to transform the energy landscape are solid-state batteries (SSBs)—a next-generation energy storage solution that promises higher energy density, enhanced safety, longer cycle life, and compact form factors. These promises are attracting immense interest from electric vehicle manufacturers, aerospace companies, consumer electronics brands, and grid storage developers. Yet, what is often overlooked amid the excitement surrounding electrolyte chemistries and lithium-metal anodes is the increasingly vital role of precision-machined mechanical components in making this revolution possible.
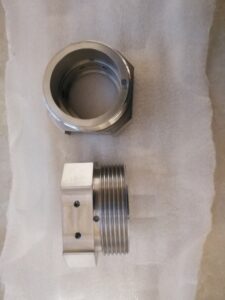
The shift from conventional lithium-ion batteries to solid-state designs is not merely a change in materials—it is a fundamental reconfiguration of how batteries are structured, assembled, and operated. Traditional lithium-ion batteries rely on liquid electrolytes, which offer a degree of forgiveness in terms of internal tolerances and material flexibility. Solid-state batteries, on the other hand, require far more rigid, controlled, and uniform mechanical environments. The electrolyte is no longer a fluid that can flow and self-adjust around electrodes—it is a solid interface that must maintain precise contact under consistent pressure to function correctly. This places extraordinary emphasis on the mechanical architecture of the battery, where every micron matters.
At the core of the growing demand for precision machined parts in SSBs lies the need to maintain extremely tight tolerances across all structural and functional components. The internal stack of a solid-state battery typically includes a lithium-metal anode, a solid electrolyte layer (which may be ceramic, polymer, or a composite), and a cathode material. These layers must remain perfectly aligned and compressed without warping or introducing stress fractures, which could compromise ion transfer or create mechanical failure points. Unlike liquid-based cells that can absorb some internal shifts, solid-state layers are unforgiving, making the flatness and parallelism of pressure plates, current collectors, and interface layers absolutely critical.
Achieving such precision is not feasible through conventional stamping or casting processes, especially in early-stage designs and low-to-mid-volume production. Instead, the industry increasingly turns to CNC (Computer Numerical Control) machining, a process capable of producing complex geometries, ultra-flat surfaces, and tight-tolerance components across a wide range of materials. The ability of CNC machines to consistently deliver precision within micrometer tolerances is not simply advantageous—it is essential for building solid-state batteries that are safe, reliable, and high-performing.
Another factor driving the increased reliance on machined components is the growing complexity of thermal management in SSBs. While solid-state batteries offer better thermal stability than traditional lithium-ion variants, they are not immune to heat buildup—especially under high charge/discharge rates or during fast-charging cycles in EVs. Efficient thermal pathways must be engineered into the battery structure to ensure that heat is drawn away from sensitive materials without creating hotspots or thermal gradients that could degrade performance. This requires the integration of heat sinks, cold plates, and thermal interface components directly into the battery housing or module. These components are often made from aluminum, copper, or specialized thermal alloys—all of which must be precision-machined to meet strict dimensional and functional criteria.
Furthermore, the electrical interfaces within solid-state battery modules are more complex and more sensitive than in traditional batteries. With higher energy density comes the need for better-controlled current paths, more robust connectors, and advanced busbar integration to manage power flow without adding resistance or creating electromagnetic interference. Busbars and terminal plates must be machined with extreme accuracy to ensure a low-resistance path and proper alignment within the battery’s spatial constraints. Precision-machined components ensure optimal contact surfaces, which is crucial for maintaining electrical efficiency and system safety.
As the industry develops new solid-state battery configurations—ranging from pouch cells and prismatic modules to custom-shaped designs for wearable devices and drones—the demand for customized mechanical parts has also increased. Machined parts are adaptable to changing designs, allowing engineers to create housings, frames, and support structures tailored to specific battery shapes and integration requirements. These parts may include mounting brackets, alignment keys, sealing interfaces, and isolation frames, each requiring specific machining strategies to accommodate the materials and tolerances needed for the application. The iterative nature of SSB development, where design changes are frequent and rapid prototyping is critical, further underscores the need for a flexible yet highly accurate manufacturing method like precision machining.
What’s more, as manufacturers transition from lab-scale prototypes to commercial-scale production, they must maintain the same level of precision achieved during R&D while scaling throughput. Precision machining enables this scalability by providing consistent, repeatable results across production runs, ensuring that performance metrics validated in early testing translate directly into commercial products. While some high-volume applications may eventually migrate to stamping or molding processes, precision machining remains essential for tooling, initial production, and continued support of complex parts that cannot be formed by simpler methods.
Materials used in solid-state battery assemblies also require advanced machining expertise. Solid-state designs frequently incorporate ceramic solid electrolytes that are fragile and must be protected from vibration, shock, and mechanical stress. Housings and protective frames often need to be made from hard metals or composites that can be difficult to work with—such as titanium, nickel alloys, or reinforced polymers. Precision machining, especially when performed with high-end tooling and coolant management systems, is capable of processing these materials while maintaining surface integrity and dimensional accuracy. The ability to handle such materials is essential for creating structural components that protect internal layers without adding excessive weight or bulk.
Moreover, the push for automated battery assembly lines further intensifies the need for exacting part tolerances. Automation relies on robotic arms, pick-and-place systems, and inline inspection tools that depend on the consistency of part dimensions to function correctly. A battery housing that varies by even a fraction of a millimeter can cause misalignment in robotic insertion or sealing systems, leading to costly rework or assembly errors. Precision-machined components enable seamless automation by ensuring every part meets exact specifications—a non-negotiable standard in high-efficiency battery production environments.
Beyond functionality, precision machining also supports the regulatory and safety compliance required in critical industries. SSBs used in EVs, aerospace, and medical applications must pass stringent safety standards, which include mechanical robustness, thermal stability, and electrical insulation tests. Machined components are not only manufactured to meet these standards but also provide traceability through documented process control, material certification, and dimensional inspection reports. This traceability is especially vital in regulated markets where failure can lead to legal liability or end-user harm.
Finally, the emphasis on sustainability and recyclability in solid-state battery development places additional importance on the precision of machined components. Many components must be designed for disassembly and reuse, requiring tolerances and surface finishes that allow for repeated assembly cycles without degradation. Moreover, reducing material waste during manufacturing is increasingly seen as a critical step in improving the environmental footprint of energy storage technologies. CNC machining, particularly when combined with optimized nesting strategies and scrap recovery systems, supports these sustainability goals by minimizing raw material usage and enabling circular production models.
In sum, the transition to solid-state battery technology is not just a materials science challenge—it is also a mechanical engineering feat. The performance, safety, scalability, and longevity of SSBs hinge on the quality of their physical components, which must meet far stricter standards than those required for previous-generation batteries. This demand for precision, reliability, and customization is creating an unprecedented need for machined parts produced by advanced manufacturing technologies like CNC machining.
As the solid-state battery industry evolves from promise to production, precision machined parts are emerging as the quiet enablers of the energy revolution. They provide the structural foundation, thermal pathways, and electrical interfaces that bring the battery’s chemical potential into practical application. Whether in the sleek housing of an electric car module or the finely-tuned interfaces of a grid storage system, these parts ensure that solid-state technology can live up to its massive potential. In the age of advanced energy storage, the future is not only solid—it is precision-machined.