Plastic has overtaken metals in the majority of the object manufacturing. Its feature like softness and expansion ability has increased its demand from customers. It can be molded into complex featured objects. Difficult holes and unbelievable curves can be carved out from plastics.
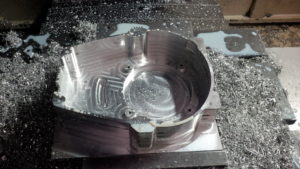
Not all plastic is favorable for molding and precision machining parts. Plastic which has a high tensile strength and high compression strength can only be chosen for molding. For example, Nylon, Peek and Ultem are good choices, but Teflon is a complete no. Customers chose plastic keeping in view their requirement and cost.
Machining is a one of the various manufacturing process specializing in cutting plastics and giving them definite shape and size. Though plastics are soft and flexible it is not easy to mold into any specific part or object. In comparison to metal machining, it poses some challenges to the Chinese machining manufacturer. Let’s discuss some of these problems.
- Plastics have a varied range of features – Unlike metals, plastics are man-made material. It is created by combining different components into a different ratio. All plastics are different with each other in consistency, strength, tolerance and color. Every customer wants to manufacture a different part with different characteristics which actually increases the technological complexity and cost while machining. Machining has to be set in the proportion of varied features each time when a customer demands something specific. Whereas metals have fixed characteristics where machining becomes fixed and easy with no variation required in design tools and customers also adjust with the features of metals making machinist’s work easy.
- The plastic is soft making it difficult to mold – Metals are rigid and that is why they are easily compatible with machining as it (machining) is favorable to rigid materials providing more resistance to deformation. Plastics, whereas, are soft and pose a threat to machinist of going out of shape while machining it. During mold temperature and pressure is set very precisely as a minute difference in setting could lead to deformation in plastics and if there would be any dis-shaping of parts then it couldn’t be assembled properly in a final stage.
- Handling is difficult – Plastic components are very sensitive, unlike metals which are rigid, tough and strong. So there is always a chance of mishandling the plastic components while machining which poses a danger to surface and corner damage. To avoid any such damage, machinist should be an expert in handling and manage the whole process in an excellent way.
- Creates a large amount of scrap – Machining of plastics is different from metal machining as it produces a huge quantity of scrap while machining. It is easy to cut by tools and that is why complex designs are created by product designers. Complex designs have more curves, joints, holes which, when put into machining creates many pieces to be cut off from the plastic creating a huge pile of scrap. Metals are not easy to cut and therefore simple designs are carved out while machining which leads to less scrap creation.
Original source is from http://www.cncmachinings.com, which is a leading china cnc machining parts manufacturer. CNC machining services are best in China. Click the link given above and explore the best options available.