Heat TREATM ENT SAFETY
Similarly as with all machining forms in precision machining parts made in china, legitimate individual insurance gear (PPE) ought to be utilized when performing heat-treating tasks. In light of the high-temperature introduction (2000°F in addition to), incredible consideration must be taken to maintain a strategic distance from serious consumes that can cause distortion and even passing.
Notwithstanding security glasses, a heat safe face shield ought to be worn to shield the face from outrageous temperatures. Heat proof gloves and a long-sleeved fireproof coat ought to likewise be worn.
Continuously utilize some kind of since quite a while ago took care of utensils to put metal in and expel it from a heater. It is a decent practice to preheat the utensils before utilizing them to expel hot metal from a heat treating heater.
On the off chance that utilizing a gas-terminated heater, consistently keep the entryway open when lighting to maintain a strategic distance from gas development inside the heater, which can prompt a blast. When lighting, likewise remain to the side of the open entryway rather than legitimately before it to maintain a strategic distance from extreme consumes from the chance of blazes stretching out past the heater entryway. On the off chance that the heater doesn’t light after a few attempts, hold up a few minutes before attempting again to permit the gas to disseminate to maintain a strategic distance from enormous, wild blazes.
When china cnc turning stainless steel parts suppliers working in a heat treating zone, consistently treat each bit of metal as though it is hot. Never expect it is sufficiently cool to contact with exposed hands. Steel at a temperature of 300°F looks precisely equivalent to steel at room temperature. A flexibly of little metal signs with “HOT” engraved or stepped on them can be utilized to help others to remember likely threat.
When extinguishing, totally lower the hot steel into the water, brackish water, or oil. Fractional inclusion when oil extinguishing can make the oil burst into flames. In the event that that occurs, never use water or a water-put together douser with respect to the fire.
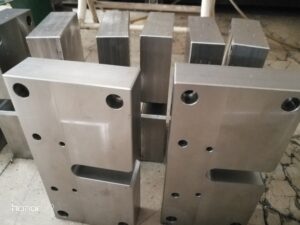
A top ought to be kept close to an oil extinguish tank so that, if there should be an occurrence of fire, it very well may be utilized to cover the tank and expel the oxygen so the fire will bite the dust.
HARDNESS SCALES AND TESTING
Since solidifying, treating, and tempering change the hardness of prepares, there should be techniques for estimating and distinguishing the degree of hardness. Two normal estimating techniques and scales are commonly used to assign those hardness levels. Both make a space in a bit of steel and contrast the size of the space with normalized scales.
Rockwell Hardness Scales
Rockwell hardness scales are normally used to assign the hardness of prepares after heat treating tasks.
Rockwell hardness testing utilizes a penetrator, or indenter, to establish a connection in a bit of material and afterward utilizes the profundity of the space to ascertain a hardness esteem. There are a few Rockwell scales that utilization various kinds of indenters and loads to perform testing. A 10-kg power, called the minor burden, is first used to situate the indenter into the material. At that point a significant burden, controlled by the scale being utilized, powers the indenter farther into the material. The distinction between the profundities of those two spaces decides the hardness.
There are a few Rockwell hardness scales, however the A, B, and C scales are the most usually utilized in the machining business. The A scale utilizes a precious stone tipped penetrator called a Brale jewel penetrator and a 60-kg significant burden. The B scale utilizes a 1/16″- distance across solidified steel ball penetrator and a 100-kg significant burden. The C scale utilizes the Brale penetrator and a 150-kg significant burden.
Rockwell hardness numbers must be associated with one of the scales. For instance, a hardness of 50 on the C scale would be composed as Rockwell C50, RC50, or HRC 50. A hardness of 90 on the B scale would be composed as Rockwell B90, RB90, or HRB 90.
Performing Rockwell Hardness Testing
There are two fundamental kinds of Rockwell hardness analyzers, the open circle and the shut circle. The open circle utilizes a deadweight framework that utilizes genuine loads to drive the indenters into the test material. The second is a shut circle framework that utilizes a microchip controlled engine to apply the power of the minor and significant burdens to the penetrators.
Before playing out a Rockwell hardness test, first set up the example for testing by ensuring it is spotless and liberated from oxidation and scale. Bogus readings can result if the example isn’t arranged effectively.
Follow these means for playing out a Rockwell hardness test on an open circle (dead weight) analyzer.
1. Watch that the wrench handle is pulled forward (counterclockwise).
2. Select the fitting blacksmith’s iron and introduce it on the hoisting screw.
3. Select the best possible penetrator for the scale wanted and introduce it in the unclogger.
4. Choose and introduce the best possible loads as per the ideal scale. Be certain they are effectively coordinated to the penetrator.
5. Spot the test part on the blacksmith’s iron.
6. Raise the lifting screw by turning the hand wheel clockwise. Proceed until the little pointer is close to the spot on the scale. At that point proceed until the enormous needle is vertical. This applies the minor burden. At that point alter the dial face so that the “0” is lined up with the huge needle.
7. Press the switch to trip the wrench and delivery the significant burden. The huge needle will start to pivot.
8. At the point when the needle stops, hold up a couple of moments and afterward return the wrench handle to the forward beginning position. This expels the significant burden, yet the minor burden is as yet applied.
9. Record the perusing utilizing the correct scale on the dial.
10. Evacuate the minor burden by turning the hoisting screw handle counterclockwise until the penetrator clears the test part.
This article is from http://www.cncmachinings.com.