A shape connection is a machine adornment that can move the cross slide either in or out as the carriage moves longitudinally along the ways. It very well may be set up utilizing either the centerline point or TPF esteem, yet knowing the TPF or TPI is useful while checking the arrangement. Both outer and interior shapes can be cut to get the china cnc machining components. Another advantage is that the shape can be cut by cnc lathe machining all kinds of precision metal parts factory utilizing the carriage power feed. Longer shapes can be cut than with the compound rest, yet length is as yet restricted by the length of the shape connection.
To set up the shape connection, follow these means.
●Lock the connection to the ways and position the carriage close to the center of the connection.
●Loosen the guide rail locking screws and change the rail to the ideal rakish or TPF setting. (One end is graduated in certificates and the opposite end in TPF.) Then reclamp the locking screws.
●Position the compound rest corresponding to the cross slide.
Since the shape connection moves the cross slide, at whatever point the course of the carriage is switched, there will be reaction from the inversion of the cross slide. Machine parts customize manufacturers china utilizing the compound rest to propel the apparatus will wipe out potential issues brought about by backfire.
Check the shape connection setting utilizing dial pointers or the machine’s advanced readout. carbon fiber cnc cutting parts manufacturers follow these means if utilizing pointers.
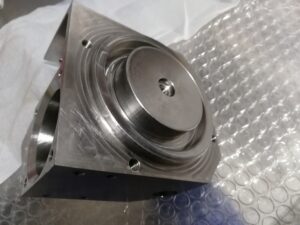
●Mount a test bar or a straight part in the machine.
●Position the shape connection so the length of the part or the test bar is inside its movement.
●Move the carriage far enough past the finish of the part or test bar to eliminate backfire, at that point move it in any event 1″ toward the path that cutting will happen.
●Mount a dive type marker on the compound rest and utilize the compound rest to carry the pointer into contact with the part or test bar to preload the marker. Set the marker on zero.
●Mount another marker to gauge longitudinal development of the carriage. Set the marker on zero.
●Move the carriage 1″ in the cutting course.
●Record the perusing on the compound rest mounted dial marker. It should be 1/2 of the TPI on the grounds that just one side of the shape setting is being estimated.
●Adjust the shape connection and rehash the check varying until the marker shows the right perusing.
Follow these means to utilize an advanced readout to check the arrangement of a shape connection.
●Move the carriage the cutting way until cross-slide development is appeared on the advanced readout. This guarantees backfire has been eliminated from the cross-slide.
●Zero both the cross-slide (X-hub) and longitudinal (Z-hub) fields of the advanced readout.
●Move the carriage another 1″ in the cutting bearing.
●Record the development of the cross slide showed on the advanced readout. In the distance across setting, the advanced readout should show the TPI. In the range setting,
the computerized readout should show 1/2 of the TPI.
●Adjust the shape connection and rehash the check varying until the X-pivot of the computerized readout shows the correct worth. This article is from http://www.cncmachinings.com/